Uncertainty and Risk
Segmentation of activities within your organisation’s supply chains is an early step to reduce the complexity of an organisation’s supply chains. Segmenting customers on the basis of ‘cost to serve’ was discussed in a previous blogpost. Here, the discussion is concerned with segmenting suppliers. But where many still regard buy price and total spend as the main focus for Procurement, it is risks that are the differentiator between suppliers.
The basis for Risk Management is Uncertainty; that is unstructured opinions concerning the supply chains of an organisation. Uncertainty is caused by Complexity within and between organisations, Variability in customer/end user demand and lead times through supply chains and Constraints in processes.
Structuring supplier risks
To convert Uncertainty into Risk requires the Supply Chains group to evaluate, analyse and rank Uncertainties. The initial step is to place an Uncertainty within one of four classifications of risk that are relevant to segmenting suppliers. These are: Supplier internal risk; Supplier location risk; Supplier’s supply chains risks and Supplier’s external risks.
Because the evaluation of Risk to an organisation is subjective, the list of possible risks within each classification identified below are examples. Checklists are available, but each business must structure its own and provide the weighted scoresheet that is relevant. Of less importance in this exercise is the annual spend that an organisation has with a Tier 1 supplier. A small supplier which provides a critical part or ingredient may have a risk profile that can be equal in score to a large supplier. The four classifications are:
- Supplier Internal risk
Financial Risks:
- Financial security and solvency
- Costs incurred for cancellation or delay of an order
- Prepared to negotiate ‘total cost of ownership’
- Global suppliers: currency and exchange rate, country inflation, interest rates
Operational Risks:
- Capability of consistent supply (delivery in full, on time, with accuracy – DIFOTA).
- Capability of supplier when affected by a supply chain disruption
- Management of supply contracts with multiple customers (the buyers)
- Volume/capacity commitments with supplier’s suppliers
- Manufacturing capability:
- Time required to allocate additional capacity to meet a buyer’s demand surge
- Operations planning capability:
- S&OP implementation status
- Customer service escalation process
- Product development capability and lead times
Contractual relationship risks:
- Supplier’s elements of Power for leverage against the buyer
- Dependency by the supplier on the buyer
- Dependency by the supplier on its suppliers
- Allocation of risk between the seller and buyer and willingness of the supplier to share risk and reward
- Data security: Buyer’s data security at supplier
- Intellectual Property (IP): supplier’s access to buyer’s proprietary knowledge regarding design, materials and technical/operations
- Complying with ESG (Environment, Social, Governance) regulations and requirements
- Environment: How the supplier evaluates an environmental risk it may face and how it manages the risk. The cost of using ‘nature capital’ in investment and financial decisions
- Social: Business relationship with supplier’s suppliers. Working conditions of its employees and at suppliers and their suppliers (the extended supply chains). Community living conditions at supplier locations
- Governance: Supplier’s leadership structure, independence of directors, executive remuneration, internal controls against illegal and unethical practices
2. Supplier Location risk:
- Major weather events: storms (hurricane, cyclone, typhoon), tornadoes, hailstorms, floods and coastal storm surges
- Geological events: earthquakes and volcanoes
- Operating risks: traffic congestion, power supply availability
- Concentration of similar suppliers at the location
- Limited number of locations for potential suppliers
3. Supplier’s Supply Chain risks:
- Connected Risk: an event that disrupts one part of a supply chains network flows to other parts, which can then interact dependently, independently and inter-dependently to affect outcomes
- Interdependent risks: events (e.g. shortage of a raw material) in an industry sector or at a Tier 2, 3 or 4 supplier may affect demand and supply in other industry sectors that supply your business
- Contingent Risk: events within a supplier’s business that could affect a supply chain e.g.
- fire at a material supplier or cargo theft from a 3PL
- concentration of assets along supply chains, such as Hub Ports and Logistics Hubs
- licence to operate a commercial business issued (and can be withdrawn) by a national government
- Emerging Risk: developments that may change demand and supply factors within an industry sector or at a supplier of items to your organisation
4. Supplier’s External risks: contained within the acronym PESTEL: (geo)Political; Economic; Social; Technological; Environmental; Legal
- (Geo) Political: Territorial claims by countries that may affect transport movements. National governments may increase protection for selected industrial sectors, which can influence supply chains, through providing subsidies, concessions, local content rules and direct investment
- Economic: International and domestic government economic policies and actions. At country level it can affect profitable revenue and the cost of doing business
- Social: Changing demographics among consumers. Identify the origin of products and ingredients (‘clean and green’). Employment and labour conditions in countries
- Technological: Availability and implementation of IT and telecommunication technologies; the potential of disruptive technologies in a country
- Environmental: Climate Change regulations; carbon emissions standards; use of eco-friendly packaging; potential of moving towards a ‘circular economy’ for products at ‘end of life’; availability and price of utilities (water, electricity and gas); renewable energy expectations
- Legal: International and country-based laws and International trade agreements
Weighted Supplier risk in segments
The Risk Evaluation in the centre of the diagram illustrates the flow for assessing risk, utilising the four Risk Classifications.
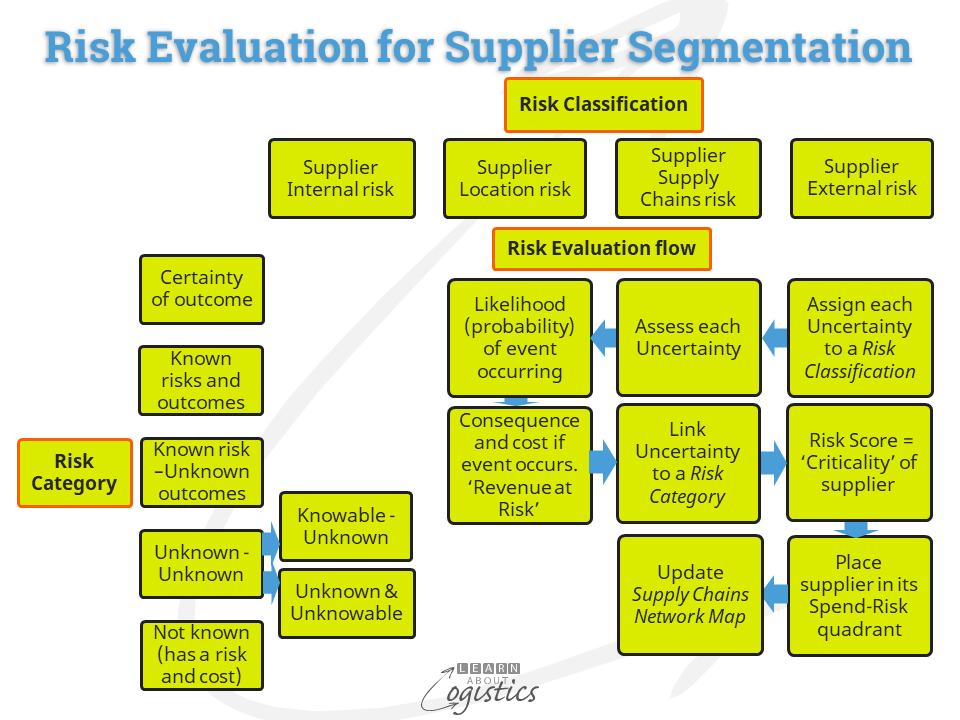
Each Tier 1 materials supplier is evaluated against the Likelihood (probability) of each event occurring and the Consequences and cost if the event occurs. The cost is measured as the potential ‘Revenue at Risk’. The Likelihood and Consequences score provide the weighted risk score, which is allocated to a Risk Category. The scores for each risk element within a Risk Classification are then aggregated to a total score for the supplier, which is transferred to the Spend-Risk chart.
The diagram is shown as a quadrant, but it can be expanded as required. On the Y axis, the level of risk is identified in the range of scores. Each supplier is allocated to a quadrant, depending on the annual spend and the risk score. This identifies the segment into which a supplier fits, which corresponds to the type of business relationship required.
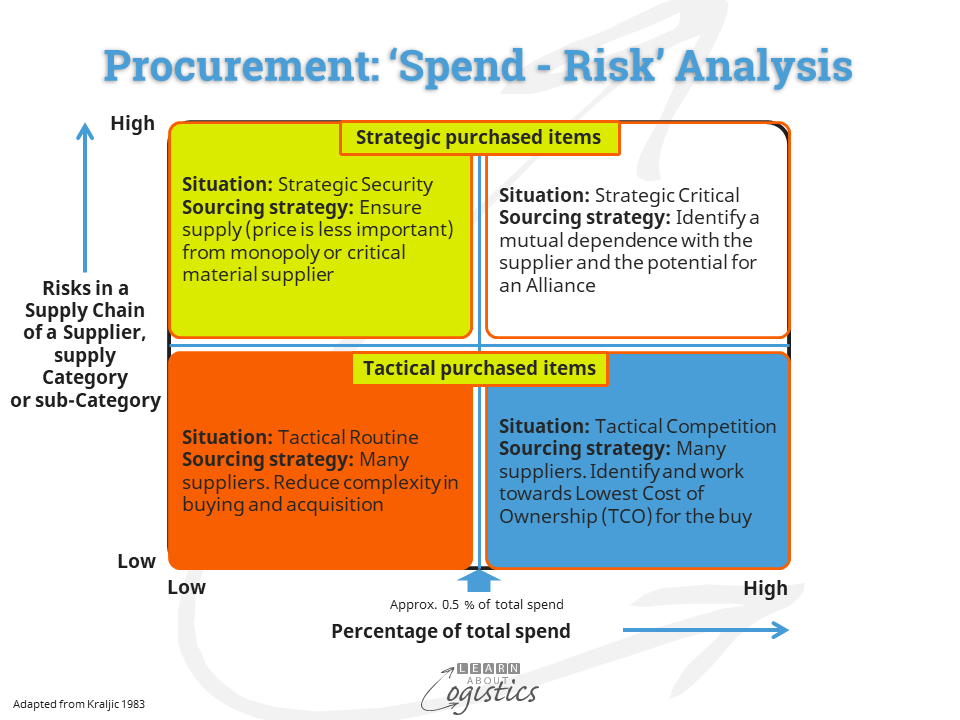
The steps identified through a Risk Evaluation for Tier 1 suppliers provides a logical flow. It supports turning Uncertainty into calculated Risks, which are allocated to segments for managing the relationship. It is an improvement on only building relationships with suppliers that incur a high annual spend, but not with small suppliers that are potentially critical to the buying business.