From Supply Network Design Map to Platforms
The less complicated it is to plan your supply chains, the more likely there will be believable plans and achievable outcomes. But the scope of international trade and the reach of organisations into countries for sales and supply means that complexity in planning is not only present, but can easily increase.
In the planning hierarchy, there is a three step planning planning process, from the organisation’s strategic business plan, through the Supply Network Map, to the tactical Sales & Operations Plan (S&OP) – it then goes to operations planning. For managers and planners to find it easier to work through the S&OP process, products need to be allocated into ‘families’, based on a similarity of operational requirements.
The term ‘product family’ is used to denote a base product with multiple variations. For example, in the confectionery industry the families can be wrapped bars, boxes of individual units, shapes for children (e.g. animals, characters in TV series) sold as individual units etc. When Hewlett Packard (HP) introduced inkjet and laser printer product families, they were designed with modular components, which enabled product differentiation to be postponed in the manufacturing process or even at region distribution centres.
It now appears that the term ‘product family’ is being overtaken by the term ‘product platform’; a term first used in the automotive industry to identify a common chassis configuration, to which different body types could be affixed.
The definition of ‘product platform’ provided by the University of Tennessee is:“The integrated system to design, develop and supply a family of products. The system includes consumer needs, products (formulas, packages), materials, process, equipment and operations”. With the Supply Chain group having responsibility for S&OP, the definition could be extended to include tier 1 suppliers and their materials/components, inventory storage and customer service operations across the core supply chains.
All these elements are similar to those used in developing an organisation’s Supply Network Design Map. Using the Map data, Product Platforms are identified based on the capacity and capabilities of resources within ‘operations’. This is because output governs what a business can sell. Capabilities are expressed as a standard unit of measure that correlates with the constraint operations resource e.g. tonnes, shippers, litres, hours, pallets, loads etc.
The number of Product Platforms will vary between 5 and 15 (preferably in a range of 6–12). The Platforms are the basis for developing and reviewing plans, using the selected unit of measure, to provide a consistent basis of communication across all functions.
Consolidating the extensive information in the Supply Network Design Map into a small range of Product Platforms for planning purposes is a major step in simplification; as is segmentation of customers, inventory and suppliers. Simplification enables an organisation to identify non-value added waste in the supply chains (and hopefully in product design). Simplification enables studies of where standardisation of materials and operations can occur within the supply chains of each product platform.
Uncertainty and Planning
Without planning, we must respond to uncertainties. However, the nature of an uncertainty is that the situation is unstructured – it has not been analysed. It is the role of Risk Analysis to take uncertainties about situations in the supply chains and turn them into structured and measurable risks, which can be managed. The previous blogpost identified a table of Supply Network Analysis and Planning (SNAP) applications, including those to assist with planning. In column 1 (which applies at the corporate and global level) is Supply Network Design Map, enabled by Risk Analysis and Scenario Planning.
To undertake and maintain a Risk Analysis within Supply Chain Risk Management is likely to be a project which consumes considerable resources. It is therefore preferable to first reduce uncertainty in the supply chains, but to do that requires identifying the causes.
Uncertainty in an organisation’s Supply Network consolidates many of the possible disruptions caused by:
- Complexity: built into processes, which are both internal (often management directed) and external
- Variability: in the patterns of demand and supply
- Constraints: limitations in the Flows of items, money, transactions and information moving through through an organisation’s supply chains
A role of the supply chain group is to reduce uncertainty and the influence of the three uncertainty elements, of which complexity can be the most challenging. The table identifies complexity in Supply Networks under four main headings.
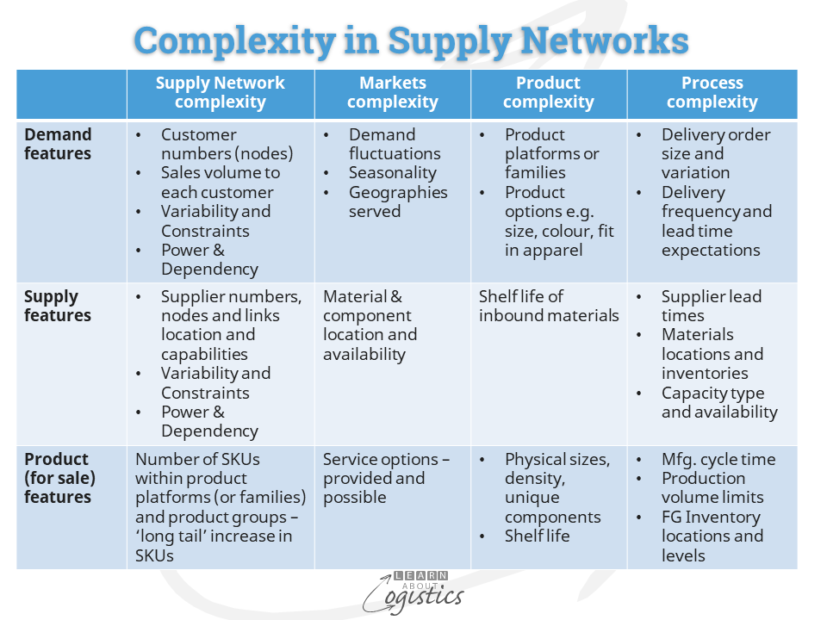
In addition to the factors in the table are those that occur through decisions outside the supply chain group, for example:
- To established or sell in more countries
- Unplanned changes to demands within regions
- Regulations affecting supply chains that change
- Mergers and Acquisitions (M&A) which increases the complexity of supply chains, often without the provision of increased resources
Supply Networks are complex, non-linear, but adaptable systems, therefore while considering effective ways to reduce complexity in supply chains, recognise that they will always be complex. Peter Senge in his 1990 book The Fifth Discipline identified longer term ‘dynamic complexity’ as being critical , rather than short term ‘detail complexity’.
Senge stated that Dynamic Complexity requires managers and analysts to:
- identify interrelationships between the elements of complexity
- understand the delays between action and consequences,
- identify patterns of change between the elements and
- ascertain why ‘obvious’ interventions do not produce the expected outcomes
But while Dynamic Complexity is being analysed and acted upon, the business must continue. This requires that the processes and actions of individuals working in supply chains should be straightforward and unambiguous, even if the outcomes become part of a complex situation.
So, to minimise the effort of the supply chain group, put your mind to simplifying the planning of supply chains by structuring the product range into product platforms. Then implement actions to reduce complexity, which reduces uncertainty and in turn, reduces the work required in risk analysis.