Operations model
The current geopolitical actions add more Uncertainty in a business, which is the driver of risk, so enterprises could be reviewing their business model. The Supply Chains group, or its functions of Procurement, Operations Planning and Logistics will provide input to the decision process. This input should provide options concerning the positioning of Operations from the perspective of ‘product types to process’, as shown in the diagram:
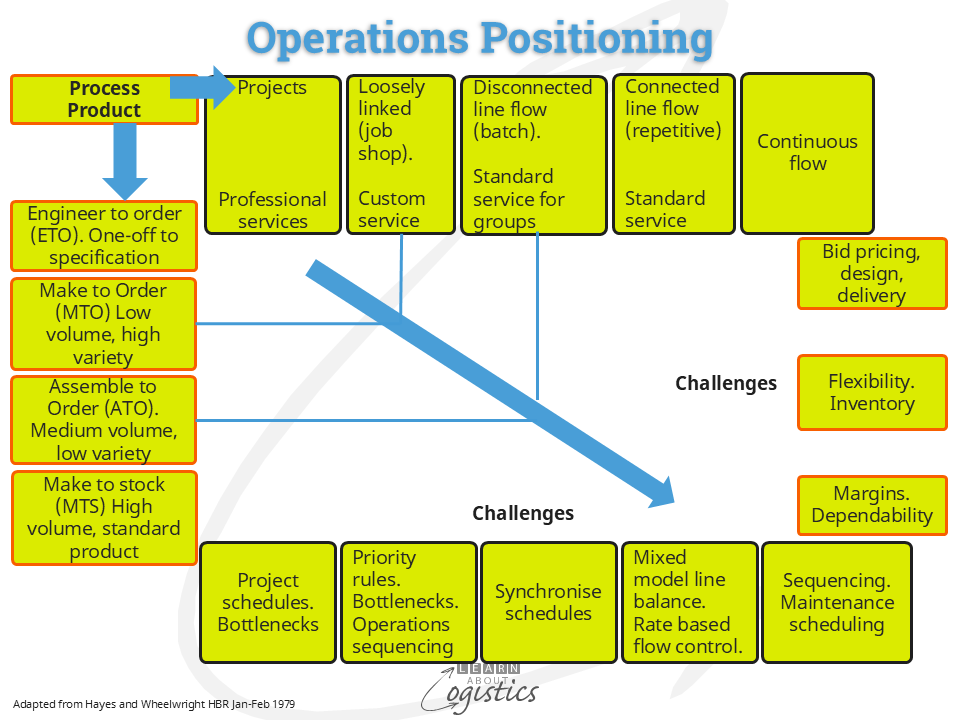
At the two extremes are Engineer to Order (ETO) and Make to Stock (MTS). ETO addresses the requirements for major, one-off projects, for which a Body of Knowledge exists and the principles of project planning and scheduling are well established and documented.
MTS relates to standard products produced from discrete materials that are assembled or ingredients that are processed into end products, co-products and by-products. Under MTS, inventory is built to satisfy the forecasts of sales, but holding inventory reduces flexibility when responding to changes in markets.
For ETO and MTO, the production focus is on the upstream process, where customers and products compete for available resources. Scheduling is mainly driven by the orders received; therefore delivery lead times can vary, depending on the load.
For ATO and MTS, the workforce and equipment are organised around the products and delivery lead times are usually short. Scheduling is driven mainly by forecasts and the availability of inventory and labour.
Business measured by turnover
There is not a universal measure to define the size of businesses. A review of definitions indicates that large multi-national companies (typically FMCG ‘fast moving consumer goods’ or CPG ‘consumer packaged goods’, governed by ‘use by’ dates), will have sales in excess of U$1b. They have the resources to manoeuvre global production capacity and inventories to accommodate changing trade regulations and costs.
Small businesses have a turnover of less than U$10m, and usually restrict their business within a country’s borders. With low buying power, they are more likely to accept higher costs of inbound materials from suppliers.
The enterprises that have the most to gain from a review of their business model and supply chains are mid-range businesses, which buy and sell across borders and are therefore exposed to changes in supply chains. The National Center for the Middle Market at Ohio State University in the US notes that the maximum turnover of a mid-size business in the US is about U$1b. In other industrialised countries, the maximum figure is likely to be about U$500m. For example, the average mid-range company in the UK has annual revenue of about U$105m (£80m).
The consulting firm McKinsey has noted that mid-range industrial businesses are likely to have four structural factors that may affect their performance: they can often compete as ‘one of many’; operations are fragmented due to mergers and acquisitions (M&A) that have assisted growth; IT systems and enterprise resource planning (ERP) applications are dispersed and there is a difficulty to attract the best talent.
However, the negatives can become positives. Many mid-range companies are often successful family businesses, where the need to succeed is more than a ‘vision and mission’ statement. Their size and more defined decision-making structure can help achieve a fast identification of new goals, with a quicker implementation that uses a good allocation of resources.
Being Agile
In the new environment, flexibility is required and being flexible is denoted as Agile. This approach works best in an environment that utilise the Process design shown in the diagram above of ‘loosely linked job shop’ or ‘disconnected line flow (or batch)’. The objective is to provide flexibility for the downstream process to achieve market demands, but provide upstream stability for planning cost-effective supply chains. The requirement is that time for production and delivery is less than the customers’ expected lead time. So, Agile works best in an environment of:
- Make to Order (MTO): Provide a design and manufacture service of options on a base product – it is the adaptation of pre-designed products. Product range is high variety (due to options) but low volume orders. The base item can be made in advance of orders, depending on the:
- expected (by customers) delivery lead time for finished items
- variability of demand for the base item
- inventory value of the base item
- range and complexity of options
- Assemble to Order (ATO): The final configuration of a product is delayed until a firm order is received from customers for pre-defined catalogue or recipe products (called ‘postponement’ or ‘delayed configuration’). The product range has less variety but higher volume than MTO. Components or ingredients are held in inventory and inventory levels are recommended by Planning, based on forecasts.
An example of MTO is manufacturing large industrial fans and extractors. The fans are designed and made in various sizes, but customers specify the frame that will support the fan, the location of motors and switches and colours. Another is a pet food company that changed from a MTS operation to MTO through using more flexible cooking and packing machines and changing the scheduling process. This initiative reduced inventory and the savings in inventory holding costs and facilities financed expansion of the business.
An extension of the MTO concept is Maintenance, Repair and Overhaul (MRO). An example is the overhaul of railway engines and jet engines, where the unit is disassembled and the parts within sub-assemblies are repaired, renewed or replaced before final re-assembly and test. Another is a business that repairs the buckets, scoops and draglines used in large scale mining operations, and where an ‘urgent’ job that can change the workshop schedule is only a telephone call away!
ATO can be used in a specialist and high-end electronics products businesses. Also a distribution facility, which packs items (typically apparel) as ‘store ready merchandise’ that can be unboxed in the retail store for display.
With an Agile mindset about internal operations, there can be an expectation that Tier 1 suppliers and 3PLs will also have a similar mindset, which may not be correct. The Supply Chains group will need to work closely with these supply organisations to establish a flexible working relationship that can respond to change.
Adopting an Agile structure within core supply chains enables a better response to changing conditions and patterns of customer demand. However, it has an ‘effective’ rather than ‘efficient’ focus, which requires acceptance by senior management and time allowed for training and implementation.