Two strategies a better approach
The role of Logistics is to provide Availability of products and services for customers. To provide Availability requires the management of inventory – incorporating policy, planning and control. Without effective management of inventory, investments in automation are wasted when handling and moving unnecessary inventory.
Change takes time. Organisations need time to move from an initial position of viewing customers and suppliers separately, to thinking in terms of supply chains, then to supply chains as a network and finally, value networks that incorporate demand and supply chains. To allow for these stages of development, construct your organisation’s Logistics strategy in two parts:
- Part 1: Strategy for operating the functions within the Supply Chains group (Procurement, Operations Planning and Logistics). This logistics strategy is a ‘bottom-up’ process for operating and improving logistics over a short term of two to three years. It is not to ‘optimize’ the function, but together with Procurement and Operations Planning, provide the most effective Supply Chains group processes that meets the customer service objectives of Marketing. The strategy structure consists of:
- the current logistics model within the Supply Chains group – how things are done
- process improvements and cost reductions to be implemented within defined time periods over the next two to three years
- Part 2: a longer term (five-year) ‘top-down’ logistics strategy for implementing change that integrates/interfaces with the Procurement and Operations Planning strategies, consolidating into the Supply Chains Network strategy. This long-term strategy takes into account agreed scenarios incorporating between seven and eleven qualitative variables (such as stability of commodity prices and freight rates, geopolitical events and suppliers’ capacity). The scenarios have an expectation range of high and low from a base.
The strategy process
Both the short and long-term Logistics strategies commence with the customers’ needs. Then work back to identify how the needs will be met, in a consistent way that meets or enhances your organisation’s profitability targets.
For the short-term strategy, the next step is to define how the Logistics processes will be governed. As a potentially decentralised operation, there needs to be a clear statement concerning under what conditions and by whom can decisions be made, preferably close to the event.
The operational Logistics Strategy plan is then developed or updated, as shown in the diagram. The black rectangles denote available policy or information and the red rectangles denote action required.:
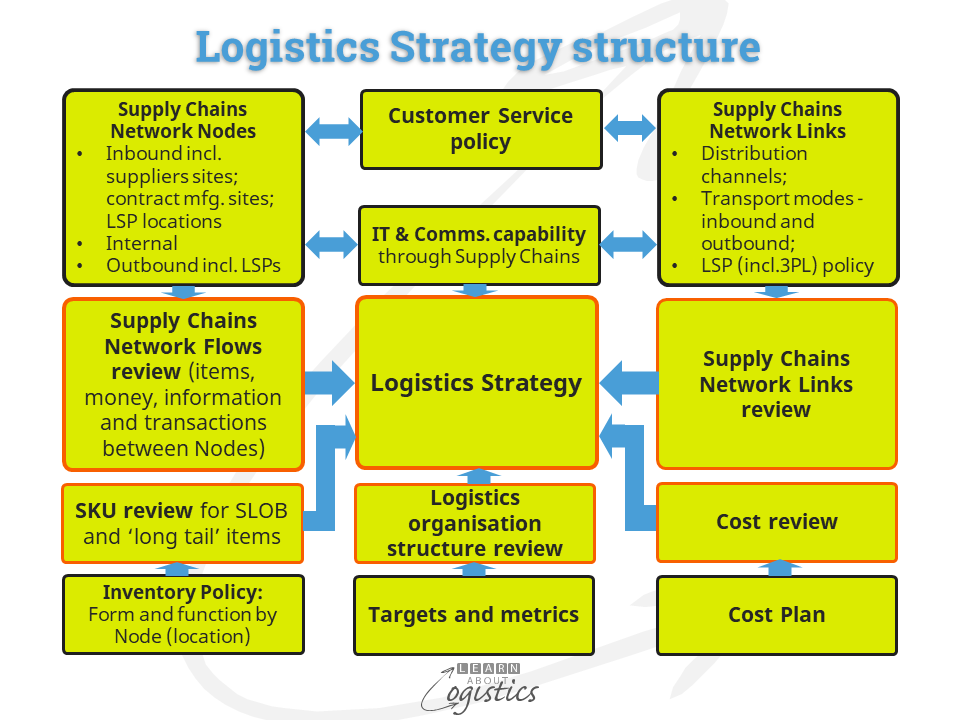
The short-term strategy recognises the current operational environment, such as sales forecast process, operations planning sequence, inventory locations and distribution process. Also, operational factors such as available production and storage capacities and supplier availability and capacity.
- Transport and distribution modes and review (Links in the Supply Chains Network) – cross-border activities – imports or exports. The location, size and structure of population conurbations being served. This incorporates considerations of distribution delivery patterns and transport modes, based on the time taken for deliveries (owned or contract fleet)
- Supplier, manufacturing and distributor locations (Nodes in the Supply Chains Network) and review of the Flows of items, money, transactions and information between the Nodes
- Manufacturing categories are Make to stock (MTS), Assemble to order (ATO), Make to order (MTO) or Engineer to order (ETO) and each has different objectives. For example, an MTS item will be a standard product with few changes, relatively consistent sales pattern and competitive pricing. Compare this with a MTO item that has non-standard configurations, an irregular sales pattern and a premium price. Many of the input materials could be the same and the products manufactured in adjacent facilities (owned or contract). However, the ‘order qualifiers and winners’ for each will differ and so will the internal and outbound logistics requirements.
- Outsourcing policy addresses the extent to which the enterprise will ‘make’ (do something within the business) or ‘buy’ (contract another party to do something). It includes the policy regarding Logistics Service Providers (LSPs), which includes third party logistics (3PL)
- Within the outsourcing policies will be considerations of global or near-sourcing of purchased items (within the Procurement strategy) and for production there is a choice of: off-shoring, near-shoring, friendly country (‘friends’)-shoring, on-shoring and in-shoring (returning outsourced activities to in-house)
- Customer service policy – the appropriate level of service for customers, identified by Marketing for each product group or market segment. Consider: order fulfilment requirements, enquiry and investigation capability and available information. For each Marketing product group identify:
- geographic location where materials, intermediate goods and finished products are, or will be sourced (Procurement strategy)
- how close to markets or raw materials the product is, or should be, produced
- how materials and products are, or should be, moved and stored
- the modes of transport in current use, plus any proposed changes
- Logistics strategy uses the accumulation of logistics requirements for the different end market segments
- The customer service policy informs decisions concerning Nodes and Links of the Supply Chains Network
- IT and Communications capability: technologies (including software) installed and required: internally or externally developed; whether (with Operations Planning strategy) to buy/rent logistics planning and scheduling applications from a single supplier or obtain multiple ‘best of breed’ applications
- Inventory location policy (Nodes in the Supply Chains Network) – centralised or decentralised inventory; location of sites; company-owned or contracted facilities; whether to differentiate facilities by fast and slow-moving stock; use of specific technologies and site layouts
- Inventory policy – the form and function of inventory by location; stock to hold for each inventory group. Review stock keeping units (SKUs) for slow and obsolete (SLOB) and ‘long tail’ products. Link with the planning approach (with Operations Planning strategy) that balances outbound products with inbound materials – preferably Sales & Operations Planning (S&OP)
- Cost plan – the cost of Logistics operations; trade-off analysis between service level requirements and cost
- Logistics organisation structure: function or flow based; allocation of responsibilities; managed or self-managed teams
- Logistics Targets and Metrics: measures of performance and achievement targets; operations improvements process and management
The strategies of Procurement, Operations Planning and Logistics are informed, then enabled by knowledge of the core and extended Supply Chains that interact with your organisation. The individual strategies are then consolidated into the Supply Chains strategy.