Effectiveness for supply chains
There remains too much of a focus in business on efficiency of the organisation’s many silos (teams, departments, groups etc). However, your customers’ concern is how the organisation’s supply chains are able to satisfy their needs – how effective is your business?
So, a critical aspect of your organisation’s supply chains is not the efficiency of individual functions, but the effectiveness of Flows that provide customers with their orders ‘in full, on time, with accuracy’ (DIFOTA). Businesses need to recognise the importance of Flows design within their supply chains, so that Logistics can focus its strategy from a Flow perspective.
The driver for effectiveness is the supply profile of your enterprise. This requires a description of the flow of items (materials, components, intermediate goods and finished goods), which identify the extent of Visibility through the ‘core’ and ‘extended’ supply chains of your organisation. This will extend (ideally) from the Tier 1 supplier’s suppliers (back to the farm and mine) through your enterprise to the Tier 1 customer’s customers (the end user) – the true ‘end to end’ objective.
The supply profile will be influenced by the range of customers’ requirements and the customers’ pattern of demand. The total description of supply chain flows also requires description about the flow of money, data and information.
The Flow of items
A Flow is a process, described as ‘how things are done’. These are identified as supply chains, of which a business could have between five and eight, typically defined by the:
- use of certain ‘critical’ materials in the Bill of Materials (BOM),
- use of particular equipment, machine assets and facilities (e.g. cold rooms) or
- specific customers (e.g. different automotive assemblers)
For a shipper business, the Flow of items has four main types:
- Make to stock (MTS):
- Assemble to order (ATO),
- Make to order (MTO):
- Engineer to order (ETO)
Although many of the input materials could be the same, the ‘order qualifiers’ and ‘order winners’ for each type will differ and so will the internal and outbound logistics requirements. Even though two businesses may, on the surface, appear to be similar in their operations, a Flow analysis may show them to be different.
To illustrate this, consider Assemble to Order (ATO). A business holds an inventory of items (in house or at a 3PL) that are picked and assembled to produce a product following the receipt of a customer order, based on a Bill of Materials or recipe. The items in an ATO business can be either discrete components (picked by each) or process materials (measured by weight or container size). A common question by customers of this type of process is “how much will it cost and when will I receive it?”
Discrete and Process ATO
Within the ATO type, consider the two situations shown in the diagrams below. A discrete components business selling, for example: electronic products, household goods or furniture and a process material business selling, for example: chemical blends, agriculture mixtures or aggregate blends. The business model of each is providing a ‘fast response’ when delivering a customer order received on-line, with the required materials and components held in stock.
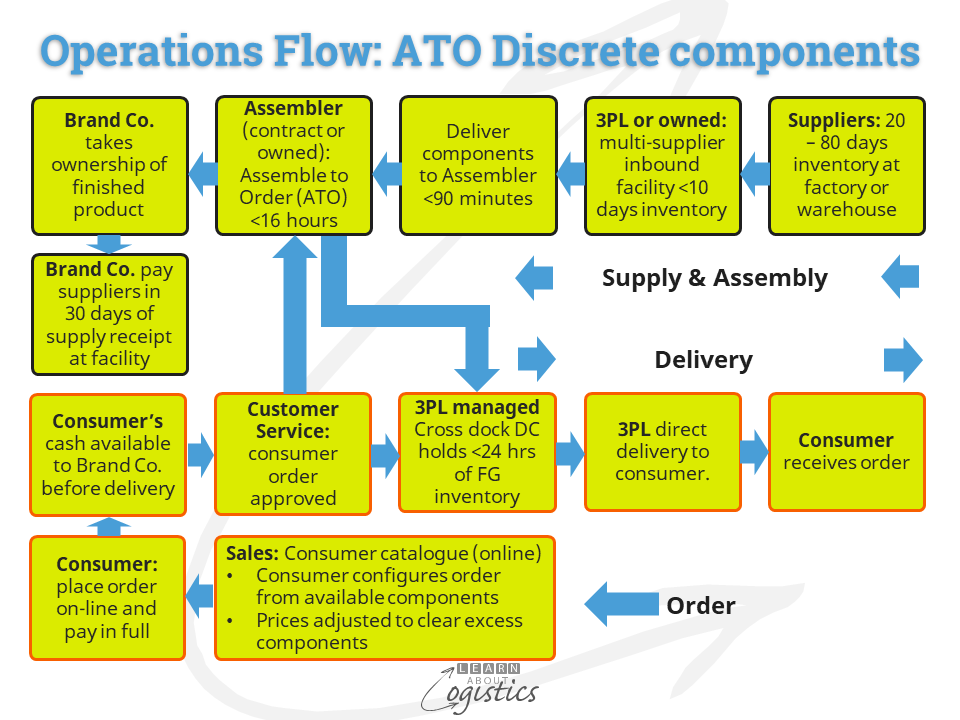
Discrete components: To achieve the assembly, test and pack time of less than 16 hours (assume Operations working two shifts) requires that the online Sales catalogue is linked to the applications for Procurement, Operations Planning & Scheduling (including inventory and order tracking), Logistics (including inbound and outbound storage facility and transport) and Finance cash flow. Assembly must be flexible in design to accommodate variable order configurations.
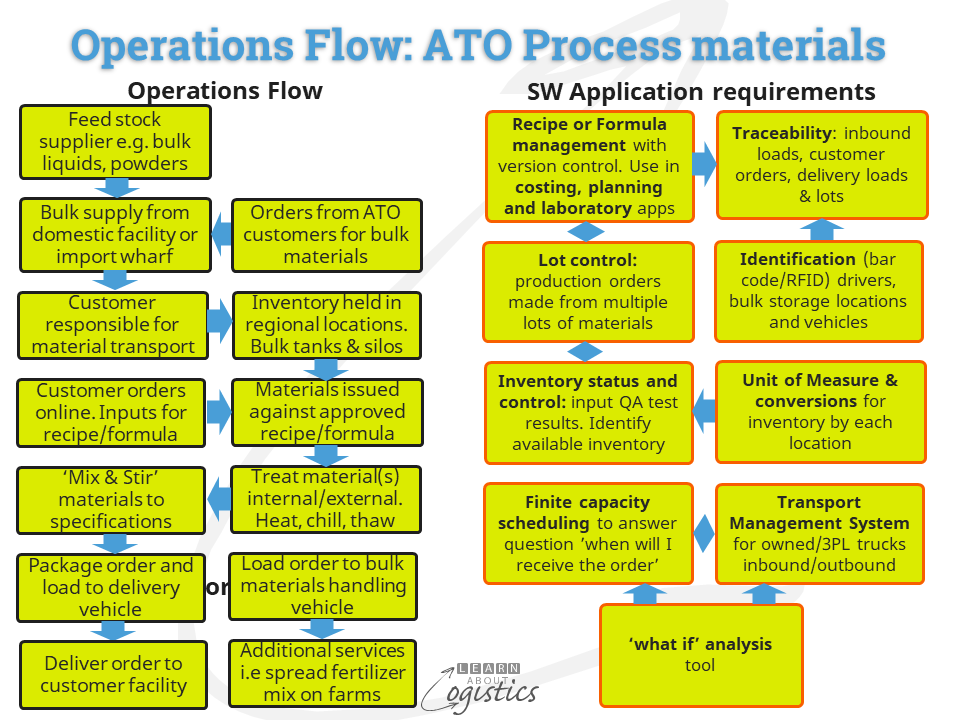
Process materials: The differences with Discrete commence with the buyer usually being responsible for the transport of purchased materials from the feed stock suppliers. There is also a delay while the laboratory constructs the recipe or formula based on inputs provided by the customer e.g. required pH for soil. There could also be a delay while some materials are transported off-site to a specialist business for treatment. Only when these materials are returned can the ‘mix & stir’ operation commence, followed by packaging and delivery or loading in bulk to specialist vehicles (owned or contracted).
Although this is an ATO business, the ‘fast response’ objective is different to the Discrete components business, due to possible delays in the process. Also, as the materials Flow for the Process materials business is different from the Discrete components business, it requires different IT applications, as shown in the diagram:
Recipe or Formula management: This is a core application that provides the instructions for materials and processes for each customer order. The application is linked with the Laboratory Management, Operations Planning and Costing applications. It is also linked with Lot Control and Traceability
Lot Control: This is a critical application as each customer order is made from multiple material lots that reflect: storage location, grade, age. and tracking of inventory movements. Lot Control is also for customer orders that have partial deliveries, with each delivery being a lot. This enables order pricing to include storage and delivery charges. Lot control is linked with Inventory status and control that depends on QA inputs from the laboratory application.
Traceability: is important for inbound loads and their storage, customer orders, outbound loads and the lots that make up the load.
Identification links to Traceability and is important if the business has contracted with one or more 3PLs for collection and delivery. Drivers, bulk storage locations and vehicles are identified (RFID and bar code), to enable accurate payments for contract drivers and the resolution of disputes.
Scheduling of Operations (production and deliveries) uses Finite scheduling for the capability to answer the customer’s question “when will I receive the order?”. To answer the customer’s question, only available materials, production equipment and vehicles can be used in the calculation.
This brief overview of different operational Flows under the heading of ATO, illustrates the importance for defining your supply chains as the actual Flows of items, money, data and information that influence your business decisions and not relying on a general definition.
Please note: Learn About Logistics will take a short break. The next blogpost will be published on Monday March 13. Thank you for reading the blogposts.