Applications for Supply Chains
Software tools and applications are enablers for gathering and storing data, then analysis and calculations; the output assists to assess options and make decisions. The most effective use within supply chains comes from tools and applications that are ‘fit for purpose’ and not a module that happens to reside in a corporate ‘integrated’ system.
The previous blogpost discussed the role and process of Sales & Operations Planning (S&OP). It stated that “S&OP is not a ‘software driven’ process… As your organisation implements S&OP, the participants will progressively define the Supply Network Analysis and Planning (SNAP) software application requirements to answer ‘what if’ questions and build scenarios”.
SNAP applications typically fit into one of three uses: Strategic Analysis and Planning; Tactical Analysis and Planning and Operational Planning and Schedules, as shown across the examples in the diagram.
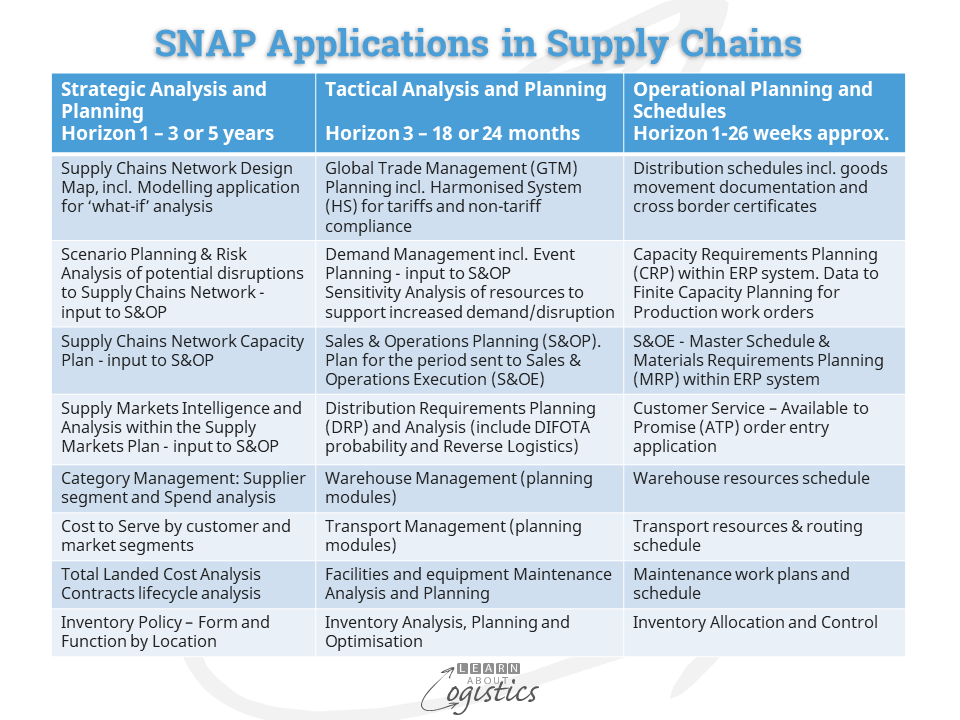
Value of SNAP applications
Most often encountered in business organisations is one or more Enterprise Resource Planning (ERP) systems, which contain modules designed to ‘integrate’ analysis, operational plans, resources, money and people. However, as companies change their business model and structures to address the more quickly evolving market needs, the installed ERP system(s), with fixed and ‘integrated’ functionality, can become a hindrance to change.
Some companies are able to affect business outcomes, due to power exercised over their suppliers and/or customers that it owns, controls or influences. However, for the majority of businesses, the complex nature of their Supply Chains Network means that predicting outcomes, establishing firm plans and managing the network is just a wish. Instead, the increasing requirement is to be more adaptable and responsive to external influences and risks that affect demand and supply.
Experiences in supply chains over the past two years and potential future disruptions has meant that having effective supply chains has become more important for organisations and therefore increases the need for SNAP applications.
Each Supply Chains Network has its own dynamics
When considering the software application required to assist in the S&OP process, start with your organisation’s Supply Chains Network Design map. This identifies the Nodes (where items are made and/or stored) and the transport Links between Nodes. Both can adapt and respond to internal events, external disruptions and actions at other nodes and links; this is without a ‘network controller’ managing, controlling or optimising the situation. Therefore, factors in supply chains that SNAP applications, designed for your S&OP process, must recognise are:
- Complex system with many interacting elements, making it near impossible to predict behaviours by entities in the Network. This is due to your organisation’s limited knowledge of the connections and relationships between:
- customers (and their customers) and suppliers (and their suppliers) and
- the network system and its environment
- Non-linear system – many ‘ifs’ and ‘thens’, as used in a Decision Tree diagram
- Uncertainty that increases with additional and global flows of items, money, data and information. Uncertainty may require additional inventory to support extended (and more variable) lead times – called Just in Case (JIC) inventory
- Constraints and Variability factors can interact dependently, independently and inter-dependently within your Supply Chains Network
- Instability in the system can result if too much ‘responsiveness’ (i.e. shorter lead times) is required. Operations. Planning must use ‘freeze periods’ in plans to avoid ‘nervousness’ in the planning process
- Adaptive behaviours by customers and suppliers that emerge as a result of interactions between the organisations and at different levels in an organisation
- Emergent and Cumulative results from these influences occur throughout an organisation’s Supply Chains Network. S&OP is a tactical planning approach that considers known, forecast and potential changes in your Supply Chains Network
As part of the Sales & Operations Planning (S&OP) process, the operational objectives must be measured:
- Availability of items for customers calculated as the probability of delivery ‘in full, on time, with accuracy’ (DIFOTA)
- Uncertainty (risk) reduction in the ‘core’ supply chains, by providing capacity buffers and/or inventory, based on strategic decisions concerning ‘form and function’ by location
Implementing SNAP applications
Improved operating systems, ‘cloud’ computing and software applications have influenced a change in thinking about implementing and managing software applications. A question when designing SNAP applications is the necessity (or otherwise) for a tight integration between planning and operational modules and applications.
SNAP analysis and planning applications are not required to be tightly integrated with applications that serve other functions in a business, especially as organisation will increasingly respond to Emergent events . Interfaced (or connected) SNAP applications maintain their own data structure, but should synchronise with the ERP database for exchange of data and information.
An example is Working Capital requirements and Cash Flow that are affected by planned changes between capacity (owned and contracted), inventory (form and function by location) and lead times – each affects the other two. This has Financial implications to be resolved in the ERP Finance module.
Data and information in SNAP applications is required on a ‘time phased, need to know’ basis – not instantaneous. There is also the potential access to unstructured data streamed from: social media, demographic maps, weather sites and customer feedback (including warranties). But again, these do not require instantaneous, on-line access.
At the Operational Planning and Schedules level, data can be streamed from the Warehouse Control System (WCS), Material Handling Equipment (MHE) and automatic identification and data capture (AIDC) instruments for automated update, analysis and reporting. The consolidated information can then be provided to planners on a ‘need to know’ basis.
The smaller and more focussed SNAP analysis applications can be implemented in months; while the more complex planning applications will take more time. In comparison, full ERP systems can take years to implement and then be considered by the users as a failure.
An approach is to have two platforms. One is the Enterprise Resources Planning (ERP) as the backbone for an organisation’s transactions. This contains the audit trail of transactions for sales order and receipts (‘quote to cash’), purchase orders and payments (‘procure to pay’), plus HR records and payroll and the accounting function. The second is the Supply Chains Network platform, containing the selected SNAP applications. As the business environment changes, rather than contemplate the acquisition of a new ‘integrated’ ERP system, only some SNAP applications would need to be upgraded or replaced.