A change in approach to risk
While many supply chain professionals will express concern about risks in their supply network, not so many take action to gain some measure of understanding and control over the risks. Given the spread and unknowns associated with the COVID-19 virus, attitudes about risks may change.
The previous blogpost discussed two foundation processes for Risk Management in supply chains: the Supply Network Map and, for critical inputs to the business, the Total Cost of Ownership These provide the necessary data and information to quantify risks in your organisation’s supply network.
Risk Analysis
The third element of Risk Management is Risk Analysis. This is to identify vulnerabilities in supply chains; where responses to events are possibly weak and alternative sources and processes required.
Undertaking a Risk Analysis is challenging, due to supply chains being non-linear operations (containing many ‘ifs and thens’), with emergent and cumulative outcomes. Also, risks in supply chains have increased with global and regional approaches to trade and the corporate emphasis on reducing supply chain costs. Some factors to consider in a Risk Analysis are:
- Demand volatility
- Demand shaping – more promotions and price specials
- Increased product lines and individual SKUs – the ‘long tail’
- Outsourcing and Contract manufacturing – often in low cost countries
- more Nodes in supply chains
- longer Links in supply chains
- Longer lead times – increased in-transit inventory and safety stock
- Increased variability through supply chains
- Constraints in supply chains
- Complexity in supply chains (the way things are done)
- Single sourcing of critical supply items
- Supply item volatility requires holding ‘safety stock’ inventory of dependent items in the Bill of Material (BOM)
In addition to analysing your Core supply chains, analysing further back through your Extended supply chains requires a more difficult investigation. However, it is worthwhile to understand the risks surrounding suppliers at level 2, 3 and 4, such as some being larger businesses than your own.
Scenario Planning
Supply chain risks can be identified through Scenario Planning, a corporate planning tool developed in the 1970s. Your organisation will have its own potentially critical supply chain scenarios, but to get started, consider about five scenarios, based on identified losses across:
- Demand,
- Supply base,
- People availability
- Transport infrastructure, capacity and mode options
- Facilities and equipment affecting capacity or inventory
- Communication failure and cyber security attack
At a residential workshop, a cross-function group of about 12 participants formed into three teams, develop scenarios and consider the outcomes. For an identified scenario event, the likelihood of it occurring and the consequences if the event happened are considered. The diagram illustrates how this enables a risk assessment.
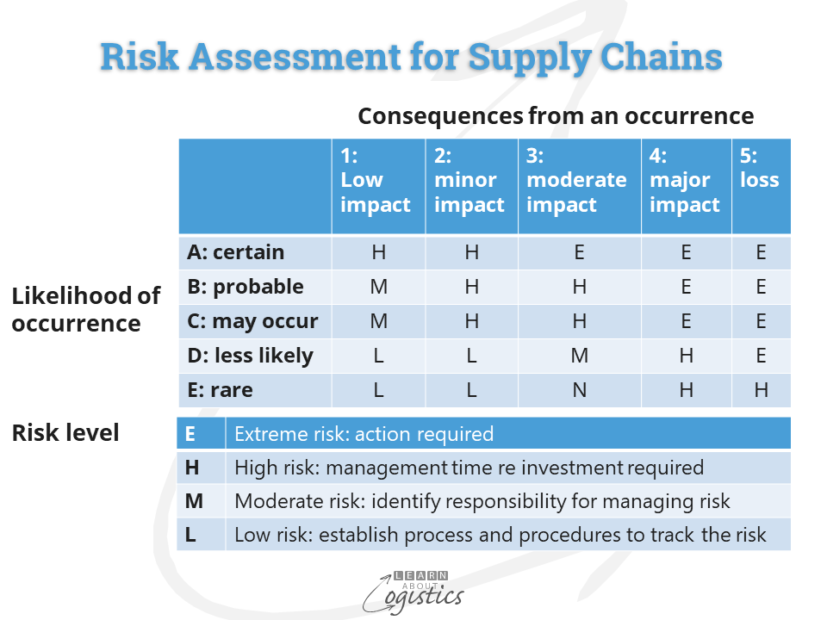
For the subsequent Risk Analysis in each situation, utilise the Supply Network Map and the Total Cost of Ownership, plus decision tree and discounted cash flow (DCF) techniques. The analysis will raise questions concerning:
- Time to recover facilities and operations from varying levels of disruption
- Supplier alternatives
- Alternatives for delivering orders – availability of 3PL and other LSP, drivers, mode and routes
- Alternative factories and warehouses
- Alternative power sources that could be available
- Alternative IT equipment and telecommunications
- Action if key staff not available for an extended period
- Ensure the safety of employees and their families
A Scenario can be modified to generate discussions around options, risks and the likely consequences. Potential modifications are:
- Expand, contract, terminate or postpone existing operations
- Phase an implementation over a longer period of time
- Invest for future growth opportunities
Actions to reduce risks
Actions to reduce supply chain risks are structured as two types:
- Mitigation measures: actions taken to reduce the likelihood of negative events occurring or affecting an organisation
- Adaptation measures: actions that reduce the vulnerability of an organisation from the effects of negative events
Mitigation measures will be specific to each organisations, but general considerations (that may also incur additional costs) are:
- Supply Chain strategy integrated into the corporate strategy
- Segment customers, inventories and suppliers
- Inventory locations and the form and function of inventory at each location
- Implement Sales & Operations Planning (S&OP) as the planning heart of the business
- Invest in supply network analysis and planning (SNAP) IT applications and the people to drive them
- Implement strategic sourcing to highlight sourcing risks
- Establish alternative suppliers for critical items (which also has risks)
Mitigation measures may also have trade-offs, where implementing a measure to reduce supply chains risks may have a negative effect on the business. An example is reduction in the product portfolio number of SKUs (therefore reducing complexity) against an investment by marketing to attract new customers with new products
Adaptation measures in your organisation must enable quick response to events of unknown scope and intensity, which could occur at any time. An approach is to use Scenario Planning to identify and enable modifications to supply chains, as markets change. Three general adaptation steps are:
- Manage the response through a cross-function emergency management centre
- Establish lines of communication with government departments and organisations that are involved with the event
- Operate the business to maximise cash flow
- Use customer segmentation to prioritise order fulfilment
This discussion has focused on analysing your supply network to identify and act against potential risks. However, these efforts will not be optimum because, while the technology is available, visibility across global supply networks (real ‘end to end’ supply chains) is not yet an easily available practice.